الف ) دیگهای بخارصنعتی (AIC / I.H.I SD TYPE)
این بویلر بعنوان بویلرهای صنعتی شناخته می شوند و دارای راندمان بالا و كیفیت بسیار مطلوب و سرعت پاسخ مناسب می باشند.
این نوع بویلرها خود اتكاء (Botton Support)، دارای دو درام جداگانه ازنوع چرخش طبیعی می باشند و قابلیت تولید بخار با ظرفیت حداكثر450 تن در ساعت می باشند.
مشعلهای این نوع بویلر در دیواره جلو بوده و به لحاظ آرایش سطوح حرارتی به گونهای است كه جریان دود بر روی سطوح بطور یكنواخت توزیع گردیده است.
كیفیت بالای حاصله از استانداردهای مطلوب و ساختارها و كارآیی بالای آنها باعث استقبال مشتریان از این نوع بویلر می باشند.
ظرفیت و شرایط طراحی
تناژ بخار تولیدی : حداكثر 450 تن در ساعت
حداكثر فشار كاری :kg/cm2g127
حداكثردمای بخار:C 515
سیستم تامین هوای احتراق : فن دمنده اجباری(Force Draft Fan)
سوخت :گازی، مایع (تك ویا دو سوخته )
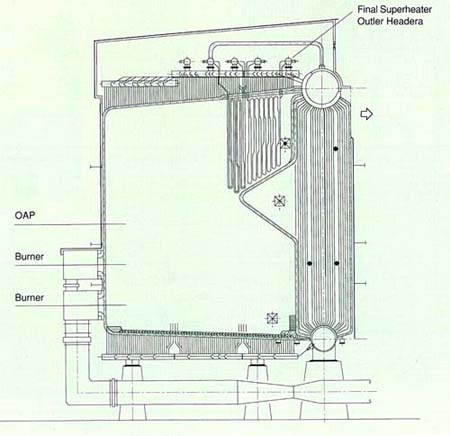
ب) دیگهای بخار یكپارچه (AIC / I.H.I SC TYPE)
از جمله مزایا و مشخصات دیگهای صنعتی عبارتست از :
بالا بودن سرعت پاسخ زمانی این بویلر به تغییرات بار
بالا بودن قابلیت اطمینان
این دیگها را می توان بطور یكپارچه در كارخانه تولید و پس از آن به سایت حمل نمود.
شایان ذكر است در مواردی كه محدودیتهای حمل بار جاده ای وجودداشته باشد می توان این نوع دیگهای بخاررا در قطعه بندیهای كوچكتر حمل نموده و عملیات نصب و برپایی را در سایت بانجام رساند. بخار تولیدی توسط این مدل دیگ می تواند فوق داغ ویا اشباع باشد و به نظر و درخواست مشتری بستگی دارد. این نوع دیگ بخار خود اتكاء (Botton Support)، دارای دو درام مجزای آب و بخار و سیستم گردشی طبیعی آب و بخار می باشد. همچنین با نوجه به آزمایشات و تجربیات فراوانی كه در طراحی و ساخت این نوع دیگ وجوددارد امكان طراحی و ساخت پیشرفته آنها فراهم آمده است.
ظرفیت و شرایط طراحی
تناژ بخار تولیدی : تا 250 تن در ساعت
حداكثر فشار بخار : kg/cm2g120
حداكثر دمای بخار : C480
سیستم تامین هوای احتراق : فن دمنده اجباری (Force Draft Fan)
سوخت : مایع گازی (تك یا دو سوخته )
این بویلر هم مصرف صنعتی و هم نیروگاهی دارد و دارای راندمان بالا و حداقل افت حرارتی می باشد. با فشار و درجه حرارت بالا كاركرده و در ظرفیت های متوسط در صنایع بكارگرفته می شود و این نوع بویلر فقط از بالا به سازه فلزی خود متصل است (Top Support) و دارای یك درام بدون ری هیتر بوده و از نوع تشعشی و دارای سیستم چرخش آب طبیعی است.
ظرفیت و شرایط طراحی
تناژ بخار تولیدی : حداكثر T/H 680
حداكثر فشار بخار : kg/cm2g150
حداكثر دمای بخار : C549
سیستم تامین هوای احتراق : فن دمنده اجباری (Force Draft Fan)
سوخت :گاز، مایع (تك ویا دو سوخته )
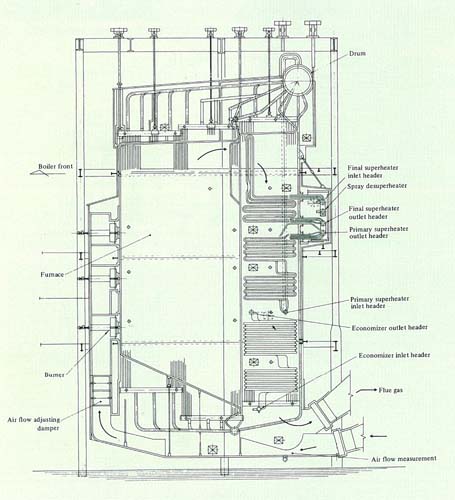
د) دیگهای بخار نیروگاهی نوع SR
این نوع دیگ برای تولید بخار در نیروگاههای حرارتی كاربرد دارد . این دیگها با سیستم چرخش طبیعی ، بطور تك درام و دارای چندین مرحله گرمكن بخار(SUPER HEATER) بازگرمكن بخار(REHEATER) و اكونومایزر می باشند.
ظرفیت و شرایط طراحی
ظرفیت : t/h 390 تا حدود t/h 2000
ماكزیمم فشار : تا حدود kg/cmg 180
دمای بخار : تاحدود C 550
سوخت : گاز طبیعی، مازوت
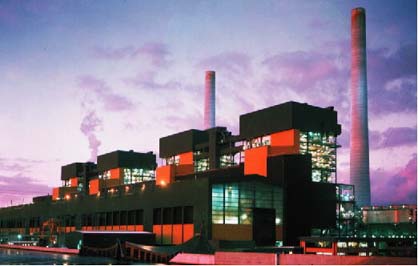
پس به طور کلی ديگ بخار دستگاهيست كه براي توليد بخار از آن استفاده ميشود. اين بخار ميتواند براي چرخاندن توربين يا گرم كردن برخي كورهها استفاده شود. در ديگهاي بخاري كه در نيروگاهها كار ميكنند به دليل نياز به فشار بالاتر بخار به صورت سوپرهيت (مافوق گرم) است. آب در اين ديگهايبخار از لوله هايي كه در ميان شعله هاي مشعل محصور شدهاند عبور ميكند اما در ديگهاي بخار كوچكتر بخار به صورت اشباع خواهد بود و در اين مشعلها شعله در داخل لوله و آب در اطراف لوله قرار دارد.
يك ديگ بخار از قسمتهاي مختلفي تشكيل شده كه توضيح مختصري در مورد آنها خواهيد ديد:
1. مشعلهاي دوگانه سوز
2. شيشه آب نما: سطح آب داخل ديگ را نشان ميدهد
3. مانومتر: فشار ديگ را نشان ميدهد
4. تابلو و تجهيزات برقي
5. هشدار دهنده : در صورت بالا رفتن فشار داخل ديگ هنگامي كه قسمتي به درستي كار نكند
6. پمپ : در اين ديگها از پمپ با دبي بالا و هد متوسط از نوع حلزوني طبقاتي استفاده ميكنند كه داراي يك الكترو موتور به عنوان محرك است..
7. دودكش : براي خروج گازهاي سوخته شده در فرايند احتراق
8. زير آب زن : خروجي از ته ديگ براي خروج رسوبات تهنشين شده در ته ديگ
9. سنسور حرارتي: از آنجايي كه بخار توليدي در حالت اشباع است و دما و فشار همواره متناسبند بهجاي استفاده از فشارسنج كه در فشارهاي بالا مشكل است از سنسورهاي حرارتي استفاده ميكنند با استفاده از اين اصل كه هر دما فشار معيني را نشان ميدهد.
10. سوپاپ اطمينان : اگر در موارد نادر تمام ايستگاههاي ايمني و همچنين هشدار دهندهها به علت نقص درست كار نكنند در صورت تجاوز فشار از محدوده قانوني خود سوپاپ باز شده و فشار را با خارج كردن قسمتي از بخار داخل ديگ كاهش ميدهد.
11. تراپ: واحديست كه بخار كندانس شده را جمعآوري كرده و به آن تله آب نيز ميگويند.
آب رساني براي ديگ بخار:
سيال اصلي استفاده شده در ديگهاي بخار آب است بايد اين سيال طي مراحلي آماده و وارد ديگ شود. قسمتهاي اصلي آبرساني عبارتند از:
1. منبع آب صنعتي مانند چاه عميق
2. ***** شني: ذرات جامد معلق در آب را جمعآوري ميكند كه از طبقات شني، سيليسي و سنگي تشكيل شده است. شير ها در اين قسمت و ***** بعدي بگونهاي طراحي شدهاند كه بعد از ساعاتي كار و كثيف شدن بتوان جريان آب را به صورت معكوس از آن عبور داد تا تميز شوند.
3. سختي گير: سختي گيري براي جدا كردن دو عنصر كلسيم و منيزيم بكار ميرود. اگر اين دو عنصر از آب جدا نشوند همان اتفاقي در ديگ بخار ميافتد كه در كتري رخ ميدهد. در واقع رسوبات سطح بين لوله هاي آتش كار با آب را كاهش ميدهد و انرژي بيشتري براي توليد ميزان معيني فشار مصرف ميشود. همچنين پاكسازي اين لوله ها علاوه بر هزينه بر بودن خط توليد را نيز متوقف ميكند.
اين بخش از دو مخزن تشكيل ميشود مخزن اول شامل بافت رزين سهبعدي بوده كه با منيزيم تركيب شده RMg بوجود ميآورد در نتيجه سختي آب از بين ميرود ولي نميتوان آن را به فاضلاب هدايت كرد چون رزين از دست خواهيم رفت. پس از مخزن دوم به عنوان مخزن احيا استفاده مي كنيم در اين مخزن آبنمك وجود دارد. واكنشهاي به صورت زير انجام ميشود زير را با تركيب رزين و منيزيم انجام ميدهد.
اكنون وارد فاضلاب شده و RNa مجددا با سولفات منيزيم تر كيب شده و توليد RMg مينمايد كه با انجام چرخهاي اين واكنشها رزين مجددا احيا شده و از چرخه خارج ميشود.
اكنون سختي آب گرفته شده ولي براي وارد شدن به داخل ديگ هنوز مشكلاتي وجود دارد
1. اكسيژن محلول در آب كه باعث اكسيد شدن خط لوله ميشود.
2. دماي پايين آب كه به ديگ بخار كه در دماي بالا است شك وارد ميكند.
براي حل مشكلات بالا از ريگازور استفاده ميكنند كه مخزني است حاوي آب بدون سختي كه از مرحله قبل توليد شده و قسمتي از بخار توليدي ديگ با فشار وارد آن ميشود تا علاوه بر بالا رفتن دماي آب اكسيژن موجود به صورت حباب از آن خارج شود.
آب موجود ميتواند مورد استفاده ديگ بخار قرار گيرد كه توسط پمپ با دبي بالا ديگ را تغذيه ميكند. اين تغذيه هم ميتواند اتوماتيك باشد و هرگاه سنسورهاي ديگ سطح آب داخل ديگ را كافي تشخيص ندادند به پمپ فرمان تغذيه دهند و يا به صورت دستي و توسط اوپراتور پمپ روشن شود.
سيستم گازرساني براي ديگ بخار:
لوله گاز شهري با يك كليد قطع و وصل اصلي وارد مدار ديگ بخار ميشود. بعد از اين كليد مانومتر فشار خط را نشان ميدهد كه حدود 5/2 بار است اما اين فشار براي مشعل خيلي زياد و خطرناك است، پس بايد از رگلاتور كه فشار شكن است استفاده ميكنيم . همچنين قبل از رگلاتور از يك ***** براي مواد جامد معلق در گاز استفاده ميكنيم سپس گاز وارد رگلاتور ميشود. با استفاده از مانومتر ميتوان دريافت فشار گاز بعد از رگلاتور به 25 ميلي بار كاهش يافته است.
گاز فشار پايين بعد از عبور از يك سوپاپ اطمينان وارد دو شير برقي ميشود كه مستقيما توسط مشعل هدايت ميشوند. شير برقي شماره يك به صورت تكضرب فقط حالت روشن و خاموش دارد كه يا گاز را قطع ميكند يا وصل، اما شير شماره دو به صورت تدريجي ميتواند ميزان گاز عبوري را كم و زياد كند. اين گاز مستقيما وارد مشعل ميشود.
مشعل:
در ديگهاي بخار معمولا از مشعلهاي دو مرحلهاي استفاده ميكنند. يك سروو موتور ميزان گاز و هواي ورودي را تنظيم كرده و وارد محفظه تخليط مينمايد. در خروجي اين محفظه دو الكترود با فاصله وجود دارند كه با عبور جرياني حدود 1 الي 10 ميكروآمپري ايجاد جرقه مينمايد تا شعله تشكيل شود. اما اگر اين جرقه تحت هر شرابطي نتواند شعله ايجاد كند سنسور نوري(سلول UV) كه در مدار وجود دارد مشعل را ريست مينمايد چون در غير اينصورت گاز در محفظه جمع ميشود كه بسيار خطرناك است.
اين مشعلها با يك رله هوشمند كار ميكنند كه تمامي قسمتهاي مشعل را تحت كنترل دارد و هر مرحله از كار مشعل (مانند فن تنها، جرقه، شعله كامل، ريست و . . .) را با رنگهاي مختلف نشان ميدهد.
در هنگام روشن شدن فن مشعل به مدت 40 ثانيه كار ميكند تا گازهاي سوخته نشده كه در محفظه باقيمانده كاملا خارج كند سپس گاز نيز وارد شده و مشعل جرقه ميزند تا شعله تشكيل شود.
تاریخچه و انواع دیگ های بخار
همزمان با ورود بشر دوران صنعتی که با استفاده گسترده تر انسان از نیروی ماشین در اوایل قرن هجدهم میلادی آغاز شد.
تلاشهای افرادی نظیر وات ،مارکیز …، از انگلستان در ارتباط با گسترش بهره برداری از نیروی بخار و طراحی و ساخت دیگ های بخار شروع شد.
دیگ های بخار اولیه از ظروف سر بسته و از ورق های آهن که بر روی هم بر گرداننده و پرچ شده بودند و شامل اشکال مختلف کروی و یا مکعب بودند ساخته شدند.
این ظروف بر روی دیوارهای آجر بر روی آتش قرار داده شده و در حقیقت برون سوز محسوب می شدند.
این دیگ ها در مراحل آغاز بهره برداری تا فشار حدود 1bar تامین می نمودند که پاسخگوی نیازهای آن دوره بود ولی به علت تشکیل رسوب و لجن در کف دیگ که تنها قسمت تبادل حرارت آب با شعله بود، و با بروز این مشکل، دمای فلز به آرامی بلا رفته و موجب تغییر شکل و دفرمه شدن فلز کف و در نتیجه ایجاد خطر انفجار می شد.
همزمان با نیاز به فشار های بالاتر بخار توسط صنایع، روند ساخت دیگ های بخار نیز تحولات بیشتری را تجربه نمود.
بدین جهت برای دستیابی به بازده حرارتی بشتر، نیاز به تبادل حرارتی بیشتری احساس می شد، در نتیجه سطوح در معرض حرارت با در نظر گرفتن تعداد زیادی لوله باریک که در آن ها گازهای گرم، جریان داشتند و اطراف آنها آب وجود دارد، افزایش یافتند. این دیگ ها با داشتن حجم کمتر راندمان مناسبی داشتند.
دیگ های بخار لوله دودی امروزی با دو یا سه پاس در حقیقت انواع تکامل یافته دیگ های مذبور می باشد.
تحول عمده دیگر در ساخت این نوع دیگ ها، تکامل از دیگ های فایرتیوپ سه پاس (عقب خشک) به ساخت دیگ های ویت یک (عقب تر) می باشد.
در دیگ های عقب خشک انتهای لوله های پاس 2 و 3 هر دو به یک سطح شبکه متصل می شوند، که به علت اختلاف دمای فاحش گازهای حاصل احتراق در پاس 2 ( 1000 درجه سانتیگراد ) و پاس 3 ( حداکثر 250 سانتیگراد ) سطح این شبکیه دچار تنش و در نهایت نشتی می شود. همچنین دیگ های عقب خشک نیاز به عایق کاری و انجام تعمیرات بر روی مواد نسوز طاقچه جدا کننده پاس 2 و 3 نیز در فواصل زمانی کوتاه دارند، که موجب افزایش هزینه نگهداری و ایجاد وقفه در تولید می شوند.
مزایای طرح لینکلن که منجر به ساخت دیگ های بخار عقب تر (WET_back) گردید، موجب شده این ساختار جدید تا امروز همه جا رواج پیدا نماید.
ظرفیت این دیگ ها حداکثر تا 4.3mw می باشد.
جهت دستیابی به ظرفیت های بالاتر، نوع دیگری از دیگ های بخار با ساختاری متفاوت بنام دیگ های لوله آبی (واتر تیوپ) ساخته شده و تکامل یافته اند. امروزه تعداد زیادی از دیگ های بخار لوله آبی با مشخصاتی نظیر فشار نامحدود و ظرفیت ها ی بالا، با راندمان 90-85 درصد جهت تولید نیرو در کارخانجات بزرگ و نیرو گاه ها و … نصب و مشغول به کارند.
انواع دیگ های بخار و طبقه بندی آنها
انواع دیگ های بخار و طبقه بندی آنها
دیگ بخار به مخزن تحت فشار بسته ای اطلاق می شود که در داخل آن سیالی برای استفاده در خارج از آن گرما می بیند. این گرما توسط احتراق سوخت (جامد، مایع، گاز) یا توسط انرژی هسته ای یا برق تولید می شود.
دیگ بخار پرفشار به دیگی اطلاق می شود که بخار آب را در فشاری بالاتر از 15psig تولید نماید. در پایین تر از فشار مذکور دیگ در گروه دیگ بخار کم فشار قرار می گیرد. دیگ های کوچک پرفشار در گروه دیگ های کوچک قرار می گیرند.
مطابق بخش یک آیین نامه دیگ و مخازن تحت فشار مربوط به انجمن آمریکایی مهندسین مکانیک یا به طور اختصار ASME دیگ پرفشار کوچک به دیگ پرفشاری اطلاق می شود که از محدوده های زیر تجاوز ننماید:
قظر داخلی پوسته 16in , حجم کلی بدون روکش و عایقکاری 5Ft3 , و فشار 100psig .
چنانچه دیگ از هریک از محدوه های مذکور تجاوز نماید، به آن دیگ نیرو می گویند. مقرارت مربوط به جوشکاری در اینگونه دیگ های کوچک به سختی دیگ های بزرگ نیست.
دیگ نیرو یک دیگ بخار آب یا بخار می باشد که در بالاتر از فشار 15psig کارکرده و ابعادش از ابعاد دیگ کوچک تجاوز نماید. این تعریف شامل دیگ های آب گرم گرمایشی یا آب گرم مصرفی که در فشار بالاتر از 160psig و دمای 2500F کار کند، اطلاق می شود.
دیگ آب گرم گرمایشی عبارتست از دیگی که در آن هیچگونه بخار آبی تولید نمی شود، لیکن آبگرم آن به منظور گرمایش در یک مدار به گردش درآمده و مجددا به دیگ باز می گردد. فشار آب در اینگونه دیگ ها را در نقطه خروجی آن نباید از 160psig و دمای آن از 2500F تجاوز نماید. اینگونه دیگ ها را دیگ گرمایشی کم فشار می نامند، که مطابق بخش 5 آیین نامه دیگ های گرمایشی از آیین نامه ASME ساخته می شوند. چنانچه فشار یا دما، از این حدود ***** نماید، دیگ باید به مانند دیگ های پرفشار و طبق آیین نامه ASME طرح شود.
دیگ آبگرم مصرفی به دیگی گفته می شود که بطور کامل پر از آب بوده، و برای استفاده خارجی، آبگرم تولید می نماید. (آبگرم دیگر به دیگ باز نمی گردد) فشار آن از 160psig و دمای آن از 2500F تجاوز نمی کند. این نوع دیگ ها را نیز در زمره دیگ کم فشار قرار می دهند و آنها را مطابق بخش چهار (دیگ های گرمایشی) آیین نامه ASME می سازند. چنانچه فشار یا دما از این حد تجاوز نماید این دیگ ها باید مطابق دیگ های پرفشار طراحی شوند.
دیگ استفاده کننده ضایعات حرارتی از ضایعات حرارتی که محصول فرعی پاره ای از فرآیند های صنعتی است، از قبیل گازهای داغ ناشی از کوره بلند کارخانه ذوب آهن یا محصولات ناشی از احتراق خروجی از یک توربین گازی، یا محصولات فرعی یک فرآیند صنعتی، استفاده می کند. ضایعات حرارتی از روی سطوح تبادل کننده گرما عبور نموده و آبگرم یا بخار آب تولید می شود.
برای ساخت این نوع دیگ ها، همان مقررات ساخت آیین نامه ASME استفاده شده برای دیگ های آتش شده بکار بده می شوند. قطعات کمکی و ایمنی مربوط به این دیگ ها بطور معمول مطابق آیین قطعات در دیگ های دیگر می باشند.
دیگ یکپارچه به دیگی اطلاق می شود که بطور کامل در کارخانه ساخته و سوار شده باشد. این دیگ دارای انواع لوله آبی و لوله دودی یا چدنی بوده و دستگاه های احتراق، تجهیزات کنترل و ایمنی را نیز به همراه خود دارد. دیگی که در کارخانه ساخته شده و سوار می شود نسبت به دیگ مشابه ای که دارای همان ظرفیت بخاردهی بوده و در خارج از کارخانه و در محل بهره برداری، نصب و سوار می شود، ارزانتر است. گرچه دیگ ساخته و سوار شده در کارخانه به طور معمول حاضر و آماده تحویل نمی باشد، ولی نسبت به دیگی که در محل بهره برداری ساخته و سوار می شود دارای زمان ساخت و تحویل کمتری است. زمان نصب و راه اندازی آن نیز نسبتا کمتر است. در کل می توان گفت که کار در کارگاه بطور معمول بهتر و قابل رسیدگی بوده و هزینه کمتری دارد.
دیگ فوق بحرانی به دیگی اطلاق می شود که در فشاری بالاتر از فشار بحرانی یعنی 3206.2psig و دمای اشباع 705.40F کار کند. بخار آب و خود آب دارای فشار بحرانی 3206.2psig می باشند. در این فشار، بخار آب، دارای جرم ویژه یکسانی هستند و به معنای این است که بخار، تا حد آب فشرده شده است. هنگامی که این مخلوط در بالاتر از دمای اشباع 705.40F دما ببیند، بخار خشک فوق داغ تولید شده که برای کار در فشارهای بالا مناسب است. این بخار خشک به ویژه برای به حرکت درآوردن مولدهای توربینی مناسب است.
دیگ فوق بحرانی به دو نوع یکسره و باز چرخشی تقسیم می شوند. هر دو نوع در محدوده فوق بحرانی یهنی بالاتر از 3206.2psig و 705.4F کار می کنند. در این محدوده خواص مایع و بخار اشباع یکسان است. هیچگونه تغییری در فاز مایع-بخار صورت نمی گیرد و از اینرو چیزی بنام سطح آب وجود نداشته و به استوانه بخار (steam drum) احتیاجی نیست.
دیگ ها را همچنین می توان طبق طبیعت مواد استفاده آنها گروه بندی کرد. گروه بندی رایج عبارت است از: دیگ ساکن، قابل حمل، لکوموتیوی (ساخت این گونه دیگ ها امروزه متداول نیست) و دریایی که به صورت زیر تعریف می شوند:
دیگ ساکن به دیگی اطلاق می شود که بطور همیشگی بر روی زمین نصب شده است.
دیگ قابل حمل به دیگی اصلاق می شود که بر روی کامیون، کشتی کوچک رودخانه ای و یا هر نوع وسیله نقلیه نصب می شود.
دیگ لکوموتیوی دیگی است که بریا کشیدن وسیله نقلیه بروی ریل راه آهن طرح می شود.
دیگ دریایی به دیگی گفته می شود که بطو معمول ارتفاع آن کم بوده و برای کشتی های مسافربری و باری اقیانوس پیما طرح می شوند. سرعت بخار دهی این نوع دیگ ها زیاد است.
نوع ساختمان دیگ ها را نیز می توان به ترتیبن زیر گروه بندی کرد:
دیگ چدنی، واحدهای گرمایش کم فشاری هستند که قطعات فشاری آن توسط ریختگری از چدن، برنز، یا برنج ساخته می شوند. این دیگ ها را بیشتر بر اساس شیوه ای که محفظه های ریختگری شده آن برهم سوار می شود گروه بندی می کنند. این محفظه ها توسط پستانک های فشاری، سوله های خارجی و پستانک پیچی به همدیگر محکم می شوند. سه نمونه از دیگ های چدنی عبارتند از:
1- دیگ های پره ای عمودی که پره ها بطور عمودی بروی یکدیگر قرار گرفته و توسط پستانک های فشاری یا پیچی به یکدیگر متصل می شوند.
2- دیگ های پره ای افقی که پره ها بطور افقی پهلوی هم قرار می گیرند. در این وضعیت طرز قرارگرفتن پره ها نسبت به هم مانند پشت سرهم قرار گرفتن برش هایی از یک قالب نان مکعب مستطیلی است.
3- دیگ های چدنی کوچک که با ریختگری بصورت یکپارچه ساخته می شوند. این دیگ ها در گذشته جهت تهیه آب گرم بکار می رفتند.
دیگ های فولادی می توانند از نوع پرفشار یا کم فشار باشند و امروزه بطور معمول از ساختمان جوشی برخوردار هستند. این دیگ ها به گروه های زیر تقسیم می شوند:
1- دیگ لوله دودی که در آنها محصولات احتراق از داخل لوله ها عبور می کنند در حالیکه آب پیرامون لوله ها را دربر می گیرد.
2- دیگ لوله آبی که در آنها آبل از داخل لوله ها و محثولات احتراق از اطراف آنها عبور خواهد کرد.
دیگ های لوله دودی بطور معمول تا ظرفیت 70000lb/hr و تا فشار 300psig ساخته می شوند. در شرایط بالاتر از این حدود، دیگ های لوله آبی مورد استفاده قرار می گیرند. دیگ های لوله دودی به دیگ های پوسته ای نیز معروفند. در اینجا، آب و بخار آب درون پوسته محبوس می باشند.
این نوع دیگ حجم بخاری را که دیگ می تواند تولید نماید محدود می کند. در رابطه با فشار پوسته های بزرگ، ضخامت بسیار زیادی را احتیاج خواهد داشت و این موضوع ساخت آنها را گران می نماید.
انبار ونگهداری دیگهای بخار:
اگر به هر دلیلی برای مدتی خارج از سرویس باشد و از ان استفاده نشود ، جهت حفاظت قسمت های داخلی و تخت فشار ان باید روشهای مناسب اتخاذ شود.
نگهداری دیگ سرد با دو روش مرطوب وخشک انجام می شود.در نگه داشتن کوتاه مدت دیگ بخار یعنی بین 24 ماه از روش مرطوب استفاده کرد اما در نگهداری طولانی تر باید از روش خشک استفاده شود.
1. نگهداری با شیوه مرطوب:
در اینگونه نگهداری دیگ بطور کامل و بدون هوا با اب پر می شود جهت از بین بردن اکسیژن موجود در اب وتنظیم ph ان بین11-10 به مقدار کافی سولفیت یا هیدرازین و امونیاک به اب دیگ اضافه شود.
استفاده از امونیاک و هیدرازین بر سولفیت سدیم ترجیح داده می شود زیرا هر دو فرار بوده و املاح اب را افزایش نمی دهد. علاوه بر این رسوبی ایجاد نمی شود، هنگام راه اندازی مجدد دیگ، احتیاجی به تخلیه صرف زمان نیست.
اضافه کردن مواد شیمیای در دیگ باید به نحوی انجام شود که از اختلاط کامل انها اطمینان حاصل شود همچنین در صورت امکان یخ زدگی دیگ، پیش بینی های لازم مانند قرار دادن المان گرم کننده در داخل یا اطراف دیگ ضروری است.
2. نگهداری با شیوه خشک:
در نگهداری های طولانی تر باید دیگ را کاملا تخلیه، تمیز ودر صورت لزوم به کمک هوای گرم کاملا خشک کرد. سپس باید با قرار دادن کیسه هایی از خشک کننده ها نظیر سیلیکاژل در داخل دیگ ان را به حالت خشک نگهداری کرد. سپس درب دیگ را کاملا بسته و از نفوذ هوا به ان جلوگیری می شود. بازدید منظم خشک کننده باید انجام شود و در صورت نیاز کمبود ان جبران شود.
مواردی که لازم است بصورت سالیانه کنترل شوند عبارتند از:
1- حداقل یکبار بازرسی وتمیز کاری
2- وضیعت شیرها از نظر باز و بسته شدن
3- میزان بودن کنترل کننده ها روی درجات مورد نظر
4- کیفیت اجرهای نسوز و در صورت نیاز تعویض انها در درب جلو و عقب
5- مرور اطلاعات ثبت شده به وسیله اپراتورها